Just-in-time ( JIT) (resurssnål produktion)
JIT kallas ibland för lean production eller lagerlös produk-
tion. Rätt sak på rätt plats i rätt tid utgör grunden för JIT.
Bilbranschen var först med att anamma JIT-tänkandet med Toyota Motors i
spetsen. I väst populariserades metoden av TQM-experterna Deming och Juran,
vilket fick företag som Ford och General Motors att ta till sig metodiken på ett
tidigt stadium.
Drivkrafterna bakom att arbeta med JIT står vanligtvis att finna i en eller fler
av följande faktorer:
1. Minska ställtider i verksamheten.
2. Förbättra ordersystemet.
3. Kortare ledtider och effektivare processer.
4. Möjlighet att producera små partistorlekar.
5. Minskade produktionskostnader.
6. Reduktion av överkapacitet.
7. Minskat behov av säkerhetslager.
8. Minska felfrekvensen i produktionen.
När organisationer tar sig an ett JIT-projekt genomförs det vanligen i kombina-
tioner av nedanstående åtgärder:
1. Köpa och producera varor i mindre partier men med högre kvalitet.
2. Utforma mer effektiva arbetsflöden och eliminera flaskhalsar i form av tid och
kostnader.
3. Se över intressentrelationer och deras påverkan på produktionsapparaten.
4. Bygga starka relationer (partnerskap) med de viktiga leverantörerna.
5. Minska andel misstag och dubbelarbete.
6. Förhindra tekniska haverier och annat som kan inverka menligt på produk-
tionen.
7. Skapa motivation och en känsla av delaktighet i produktionsprocessen hos de
anställda.
Arbetet med att effektivisera de produktionsrelaterade flödena har visat sig med-
föra en rad effekter av delvis oväntat slag, som:
1. Stora lager ökar inte servicegraden. Slapphet i systemet och brist på precision
gör att lager, tvärtemot den konventionella klokskapen, inte främjar service-
nivån.
2. Produktiviteten ökar med knapphet på resurser. Högre krav på precision gör
att tidhållning och kvalitet ökar, vilket medför ökad effektivitet.
3. Motivation och arbetstrivsel ökar genom ökade krav på arbetsprecision och
tidhållning, vilket kanske är något överraskande.
4. Kvaliteten förbättras. En anledning till detta är att fel i JIT-systemet får all-
varliga konsekvenser, varför observationer av fel ökar dramatiskt.
5. Resursåtgången reduceras, inte bara genom minskad kapitalbindning utan
även i form av lägre kostnader för fel samt högre arbetsproduktivitet (som
tidigare nämnts).
JIT har fått sitt största upptagningsområde vid serieproduktion inom tillverk-
ningsindustrin. Effekten blir ofta att lagerhållningen skjuts bakåt i integrations-
kedjan till underleverantörer. JIT-metoden kommer bäst till sin rätt när följande
förutsättningar föreligger:
• Väl förutsägbara volymer per tidsenhet.
• Korta ledtider.
• Relativt stora kvantiteter.
• Jämn avsättning.
• Repetitativa arbetsmoment.
Avslutningsvis presenterar vi en del av den kritik som JIT-konceptet har fått, här
förmedlad av Michael CVA från Sloan School of Management. Han lyfter fram
ett antal begränsningar med metoden som många företag i dag har erfarit:
1. Att leverera i precis tid har åstadkommit kolossala trafiksvårigheter. Arbetare
i fabrikerna står sysslolösa medan de väntar på de delar som behövs för pro-
duktionen.
2. När japanska företag expanderar i andra länder så kan de inte alltid hitta
leverantörer som omfattas av de normer som gäller för JIT. JIT förutsätter
perfekta relationer med leverantörerna.
3. Kortare produktlivscykler och ökade krav på variation ställer till problem för
JIT-produktionen, som kan ha svårt att hantera den flexibilitet i val av leve-
rantörer och de ständiga produktionsomställningar som blir nödvändiga.
Fortsätt läsa kostnadsfritt!
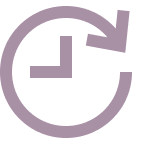
Vi behöver bara en minut…
Så roligt att du vill fortsätta läsa våra artiklar! Det får du strax göra, utan att betala något.
- Tillgång till våra låsta artiklar och webinar gratis och utan tidsbegränsning!
Dina uppgifter delas aldrig med tredje part. Läs vår integritetspolicy här.